Custom Carbon Fiber Bucket Seat & Ergonomics Jig
Made for MIT Motorsports MY24
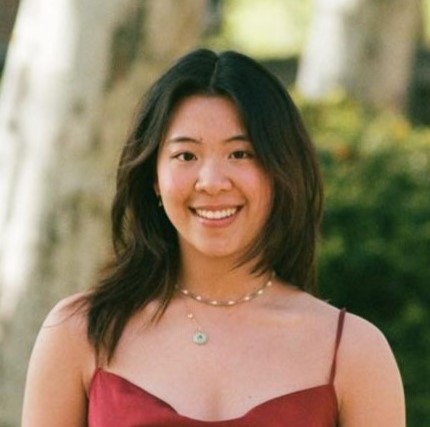
- Mia Chen
- 2 min read
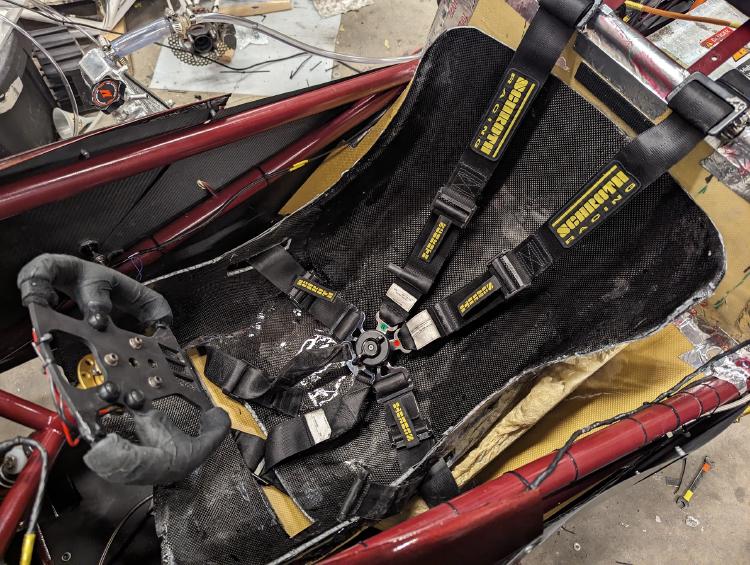
This year, I designed and manufactured MIT Motorsports’ first custom carbon fiber driver’s seat
Ergonomics Jig
To determine the optimal angles and position for our driver, I designed an ergonomics jig with adjustability for the driver position as well as the position of the steering wheel, pedalbox and headrest relative to the driver.
Ergonomics testing with our main driver
The angles found through ergo jig testing with our tallest and shortest driver were directly reflected in the locations and angles of the frame tubes, providing platform for the firewall and seat of our car.
Custom carbon fiber seat
Calculations
The carbon fiber seat was designed to withstand the the maximum braking, cornering and acceleration load cases. The layup schedule (number of plys of carbon fiber, thickness of core) was determined by calculating bendings stress and maximum deflection at places in the seat that would be experiencing the highest loads.
load cases
Sized for driver egress loads, up to 2 G of impulse force
cornering loads on side panels
I ended up manufacturing two seats with two different mold. The first was a bead seat mold where I had our driver sit in a vacuum bag full of epoxy and foam beads to conform the mold to his shape. The second method was a cnc foam mold that I machined out of pieces of insulation foam and then stacked and bonded together. These were both manufactured in-house with wet layups and I used two plys of carbon fiber on each side and a 4 mm core. We ended up choosing the seat manufactured with the bead seat mold becuase the organic shape was more comfortable for the drivers. Below are some pictures of the manufacturing process!
For more details about calculations, design requirements, and the manufacturing process take a look through the seat design binder:
- Tags:
- Motorsports
- Mit