Manufacturing of an FSAE Steel Space Frame
Welding and jigging the frame for MY24
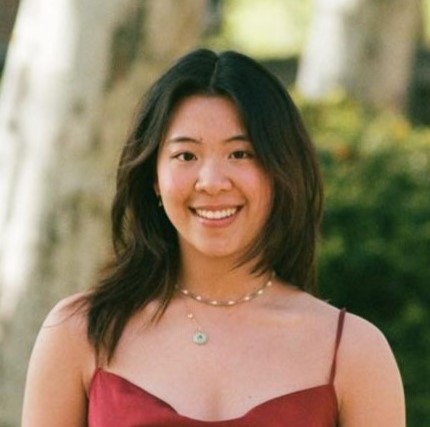
- Mia Chen
- 2 min read
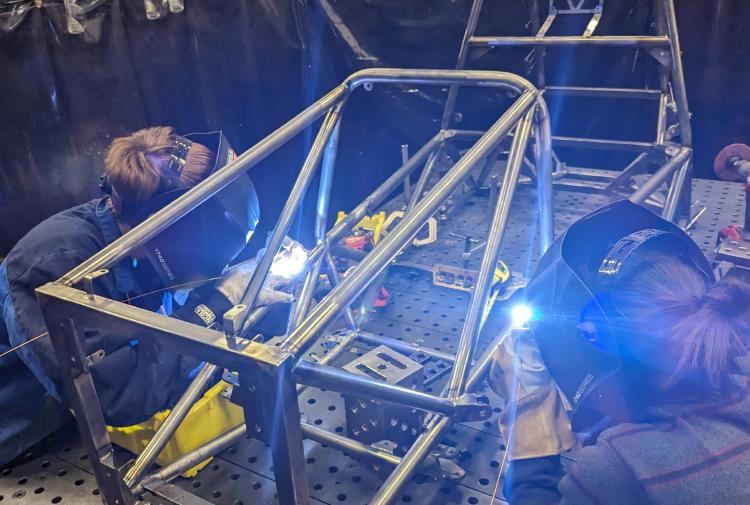
Introduction
One of things that I told myself I had to learn in college was how to weld…so that’s exactly what I did. I started learning TIG welding in the fall and practiced for a few hours each week, at first just welding straight lines and then gradually moving on to butt joints and lap joints. Some pics of my progression from dull crooked worms to “stacking dimes” (as I’d like to believe) can be seen below:
Frame Manufacturing
By IAP (MIT’s Independent Activities Period, also when we do the bulk of our manufacturing for motorsports) I was ready to help weld the car. Our team consisted of two welders (me an another freshman) and around 4 other people to help with jigging the frame tubes to precise angles and distances before we welded them. As manufacturing went on, jigs became more and more complicated and required more planning. Some of my personal favorites were this one for the front hoop of the car:
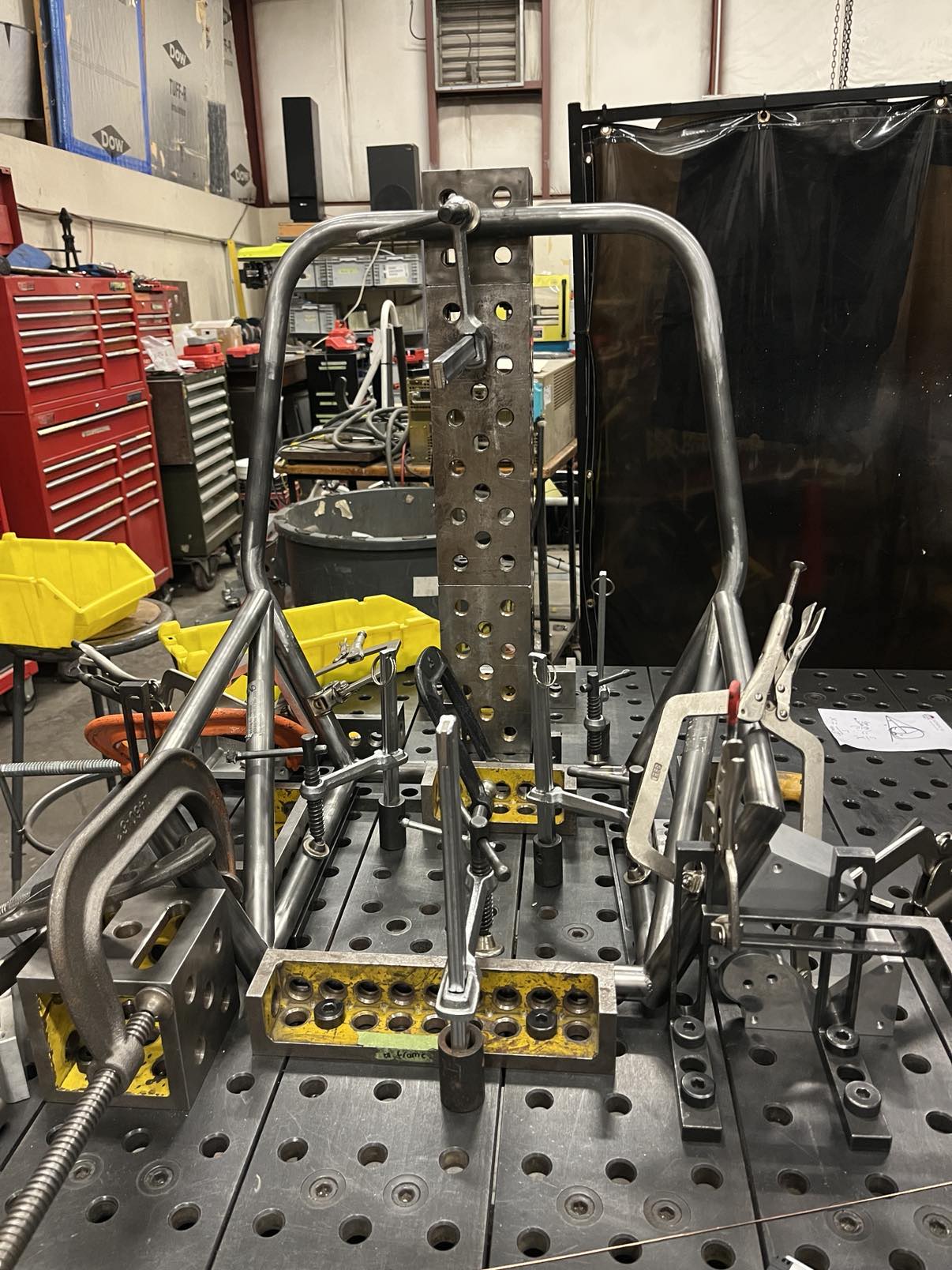
And the main hoop and rear basket jig, when it started to really feel like the car was coming together:
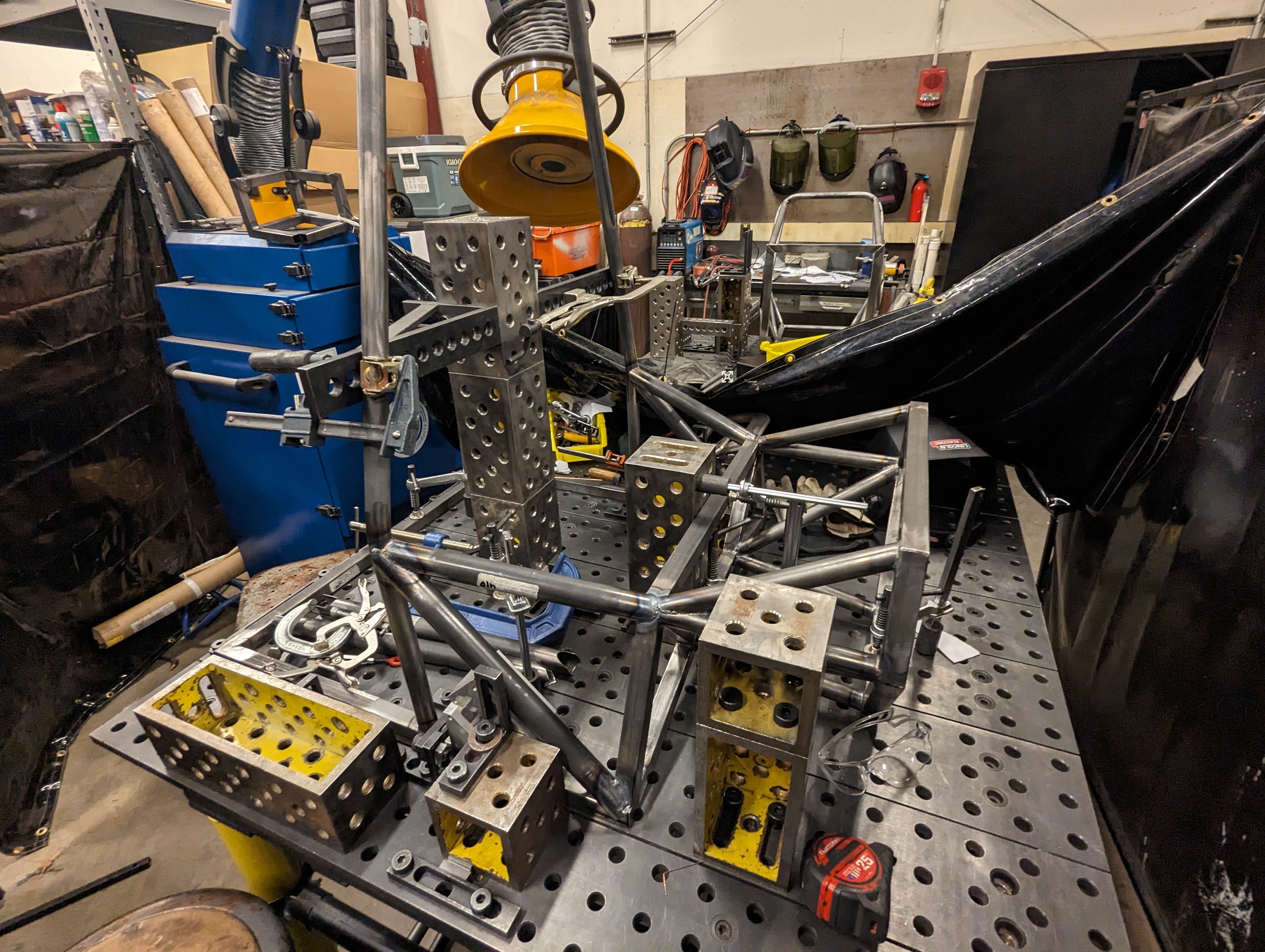
IAP was grueling, but it was a lot of fun, and after eight days of welding from morning to night we finished all of the tubes in the frame!
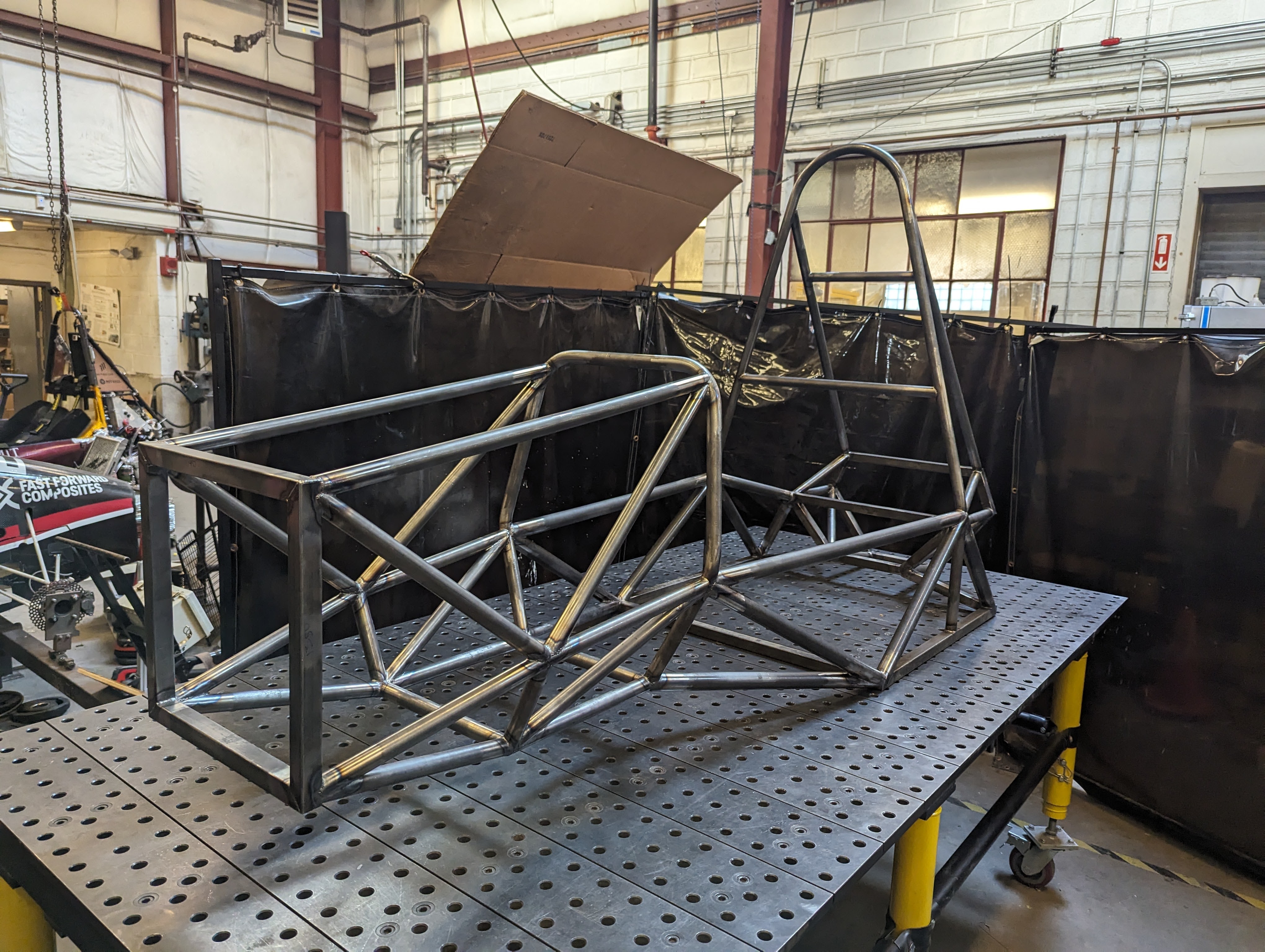
The tabs for mounting all the other systems on the car took longer since we had to wait on the systems to give us designs and mounting points, but we were able to get everything welded, send the frame out for powder coating (there was some sisagreement about the shade of red we picked but it was a democratic vote) and assemble the car in time for Rolling!
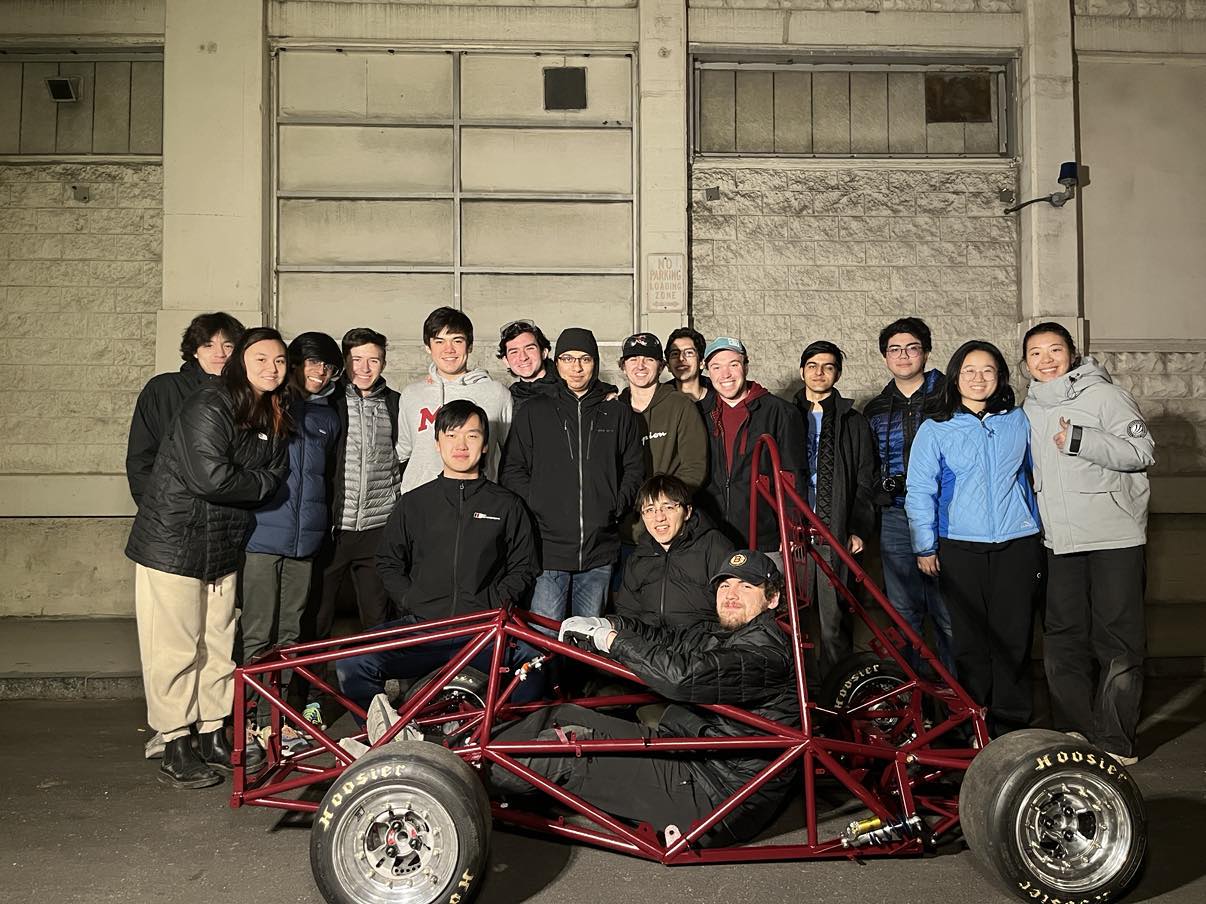
Next year I’ll be the frame lead so I’ll be not only helping to manufacture the frame but I’ll be the one designing it. However, I still look forward to the IAP manufacturing grind (and to training the incoming freshman to build myself a welding and jigging army)!
- Tags:
- Motorsports
- Mit