Finite Element Analysis of FSAE Space Frame
Validation of Torsional Testing Data
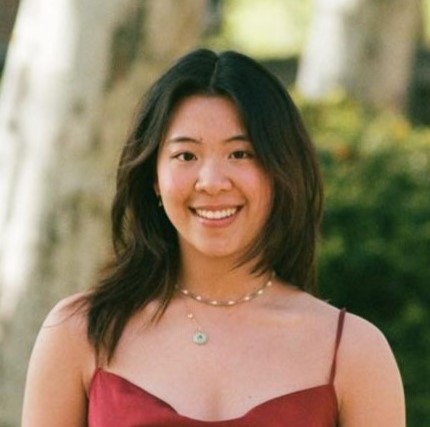
- Mia Chen
- 2 min read
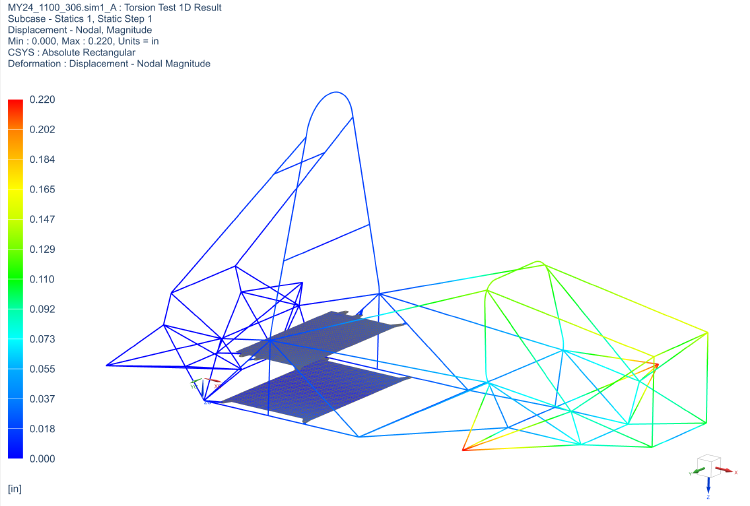
Validation of MY24 Frame Torsion Testing
Last season, we tested the torsional stiffness of our steel space frame by twisting it in a torsionation jig. This year to help me design the MY25 frame, I modeled MY24 in FEA and twisted it the same way to validate our torsion testing.
We torsionated three times, once with a minimum rules viable frame, a second time with added diagonal braces, and a third with the braces and the battery.
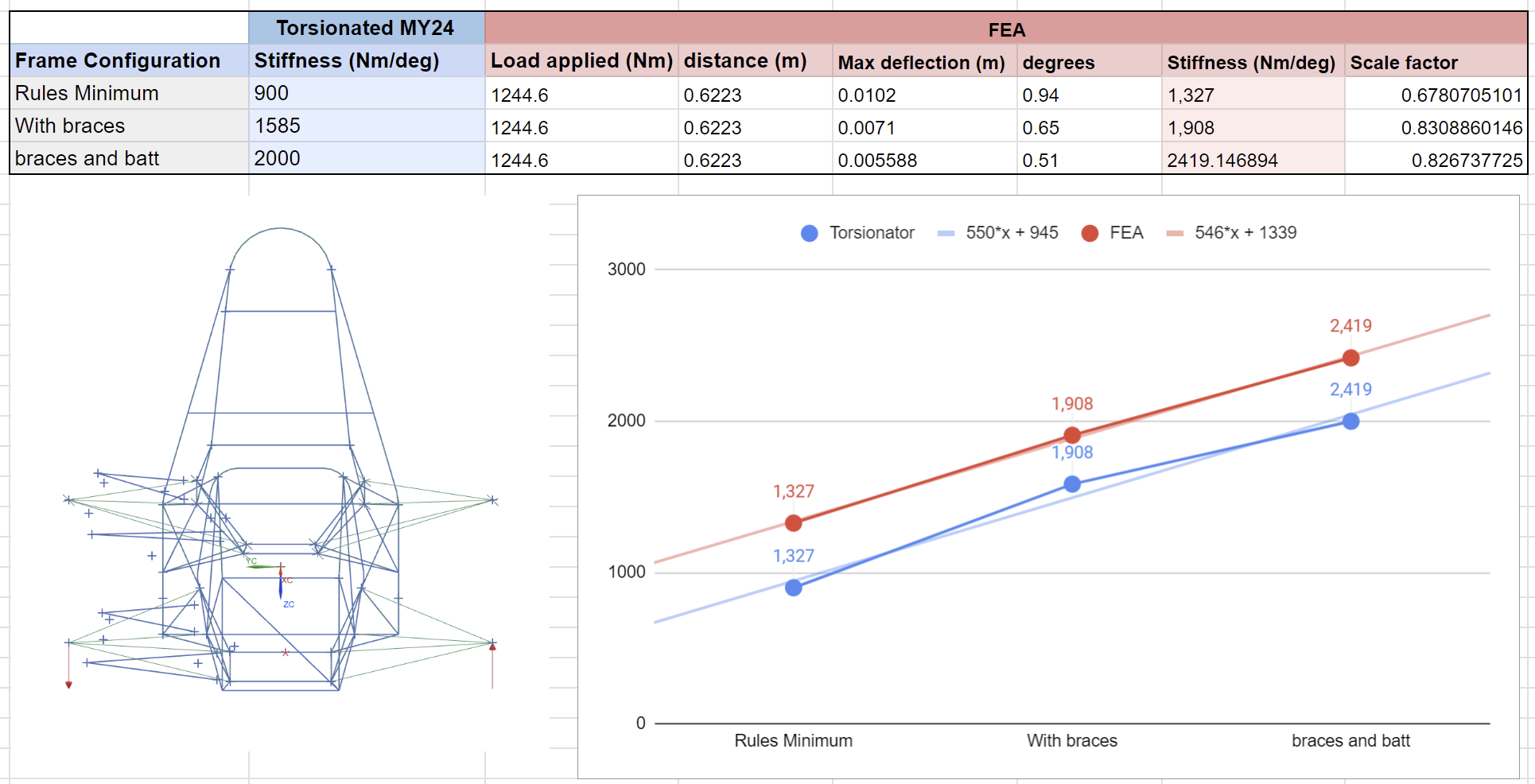
To correlate this data, I did one dimensional FEA on the frame for the same three configurations. I modeled the battery as just the top and bottom aluminum structure plates rigidly mounted to the frame. The results of the FEA correlated very well with our physical torsion testing, with a roughly 78% scaling factor between simulation and experimental values. This difference can likely be attributed to the 1D nature of the simulation, since it does not take into account the bending of the frame tubes that contribute additional compliance to the frame. The next step would be to develop a 3D model, but I now know that a 1D model provides a pretty good reference for the relative stiffness of different frame designs that will enable rapid design iteration for the MY25 Frame.
Sneak peek of the MY25 frame so far:
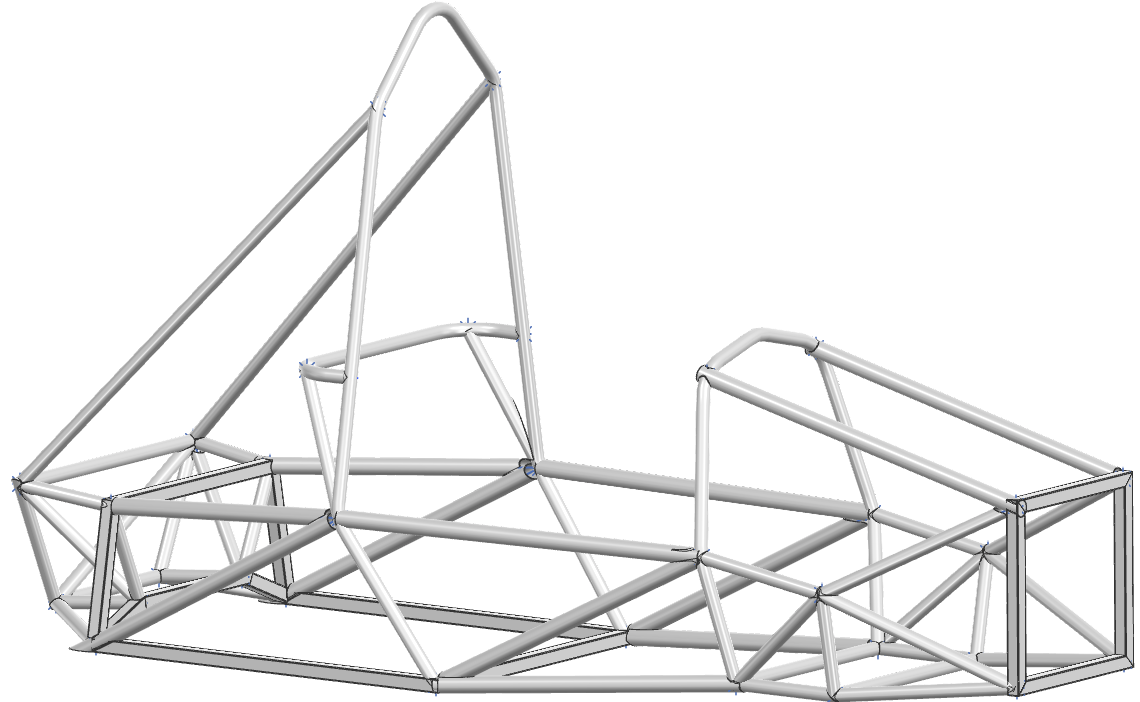
- Tags:
- Motorsports
- Mit